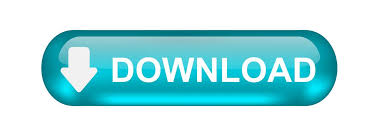
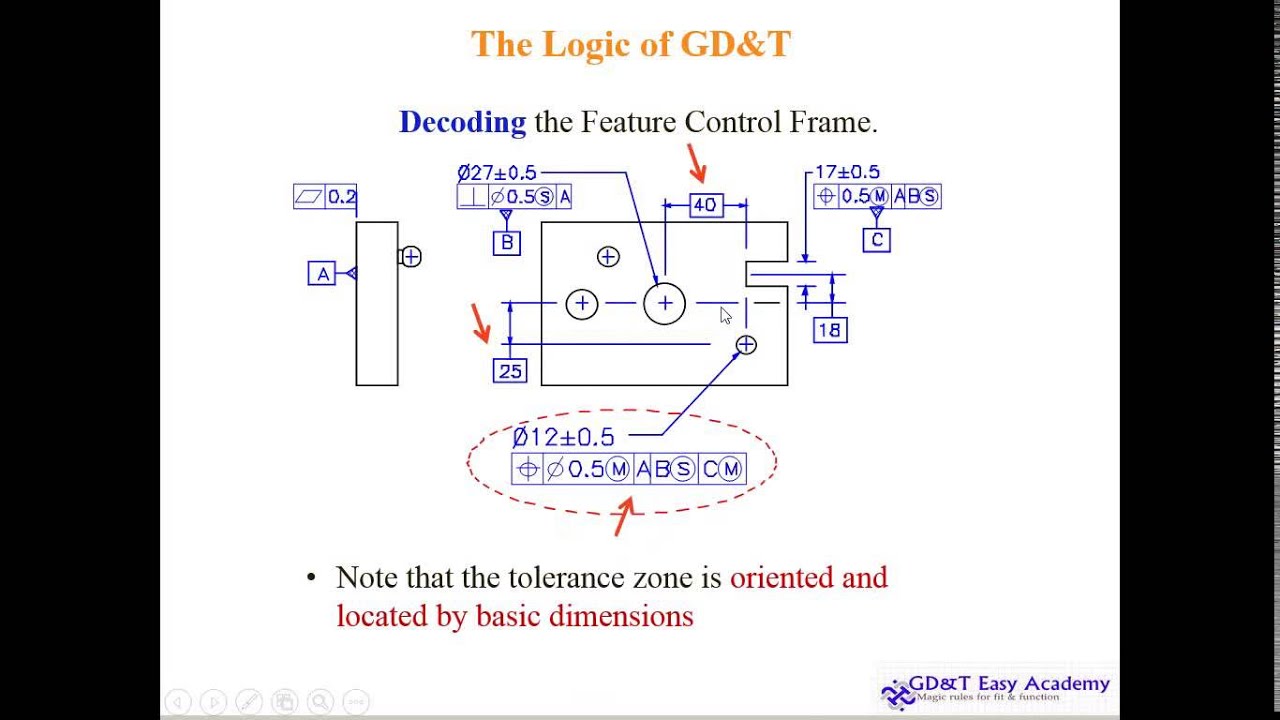
Describe profile tolerance basic concepts and applications*.Perform position tolerance (RFS and MMC) special application and calculations*.Interpret applications of datum targets, size datum features (RMB), and size datum features (MMB).Interpret the various types of tolerance (flatness, straightness, circularity, cylindricity*, perpendicularity, parallelism, angularity*, position, runout, and profile).Describe the concepts of worst-case boundary, virtual condition, and bonus tolerance.Recognize the symbols and modifiers used in GD&T.Interpret the general dimensioning symbols*.Describe the types of dimensions, tolerances, and notes used on drawings.Explain the importance of standards on engineering drawings*.Learning ObjectivesĪfter completing this advanced-level course, you’ll be able to: For more complex GD&T topics, like the expanded use of composite position and profile tolerances, customized datum reference frames, the translation modifier, and applying GD&T to non-rigid parts, see our Advanced Concepts of GD&T course. This course provides a complete look at GD&T Fundamentals. The Fundamentals of GD&T Using Critical Thinking Skills (ASME Y14.5-2009) textbook by Alex Krulikowski.Newly acquired learning is reinforced throughout the class with more than 150 practice exercises, including more than 50 application problems. Additional thinking skills of application (applying the knowledge to a drawing).Examples of inspection methods for each geometric tolerance.Related and unrelated actual mating envelope.Discussions of verifications principles for each geometric tolerance.General dimensioning symbols, including radius, controlled radius, spherical radius, diameter, spherical diameter, square, counterbore, spotface, depth, countersink, 'by,' maximum dimension, minimum dimension, reference, dimension origin.Interpreting cylindricity and angularity.Additional terms, concepts, and symbols used in GD&T.This in-depth, advance-level course also covers This class includes all the topics from the Fundamentals of GD&T 2-day foundational-level class: an explanation of geometric tolerances, including their symbols, tolerance zones, applicable modifiers, common applications, and limitations Rules #1 and #2 the datum system form and orientation controls, tolerance of position (RFS and MMC) runout and profile controls. The course can be conducted in three 8-hour sessions or with flexible scheduling including five mornings or five afternoons. Just agree to make your design intent clearer in the future and leave it at that.This 3-day Fundamentals of GD&T course provides an in-depth study of the terms, rules, symbols, and concepts of geometric dimensioning and tolerancing, as prescribed in the ASME Y14.5-2009 Standard. Politics is rarely an engineer's strong suit. A shared cost if you gain added benefits would be a reasonable compromise. Since this is a tool-safe error anyway, it really is a reasonable consideration to tweak the mold along with whatever other changes may be beneficial. My opinion, the vendor should have confirmed and should fix the part. In the end, none of us will end up in court having to defend the right way to interpret ASME Y14.5 or ASME Y14.41. If this is a one off and you really don't expect future business with this supplier, you can push it harder, again, through the purchasing department. If you value this supplier, you have purchasing strike a deal and chalk it up to experience. In the end, I find that these kind of arguments fall under the heading of "partnership agreements". Not knowing the design intent, it is difficult to know what the "right" way to define this really is. Variation of that angled face will vary significantly if the radius tolerance is even 20% of 0.5mm. In design, this is very poor control of the angled surface if its position on the diameter is indeed a design element where the overall OD is not as significant. The vendor is right in that rounds are typically calculated later and are not a critical element. In this case, I too would have put a clarifying view on the drawing or a reference dimension of the smaller diameter. The part was made using an assumption that was not factual or supported by the submitted drawing.Īll "proper" interpretations are already covered.
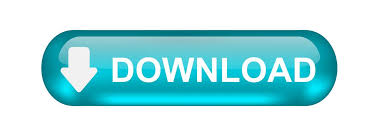